It was still light outside, but the flame is such a brilliant
white, the camera automatically adjusted to give this shot.
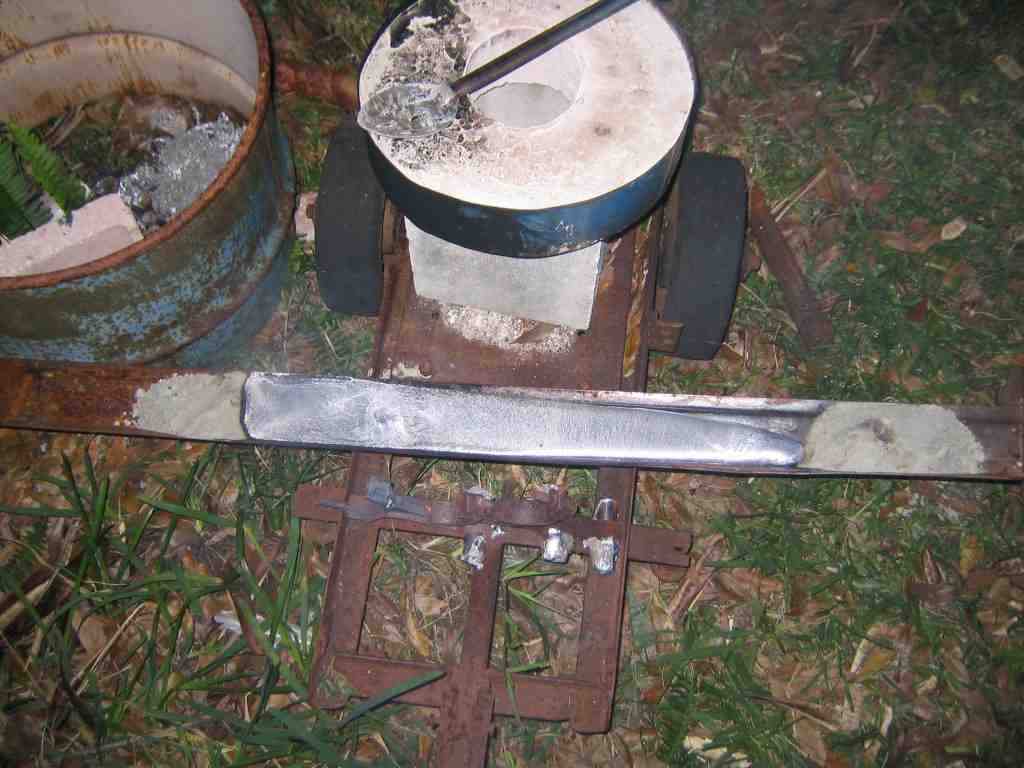
In my haste to set the ingot mold back up, I neglected to
level it.
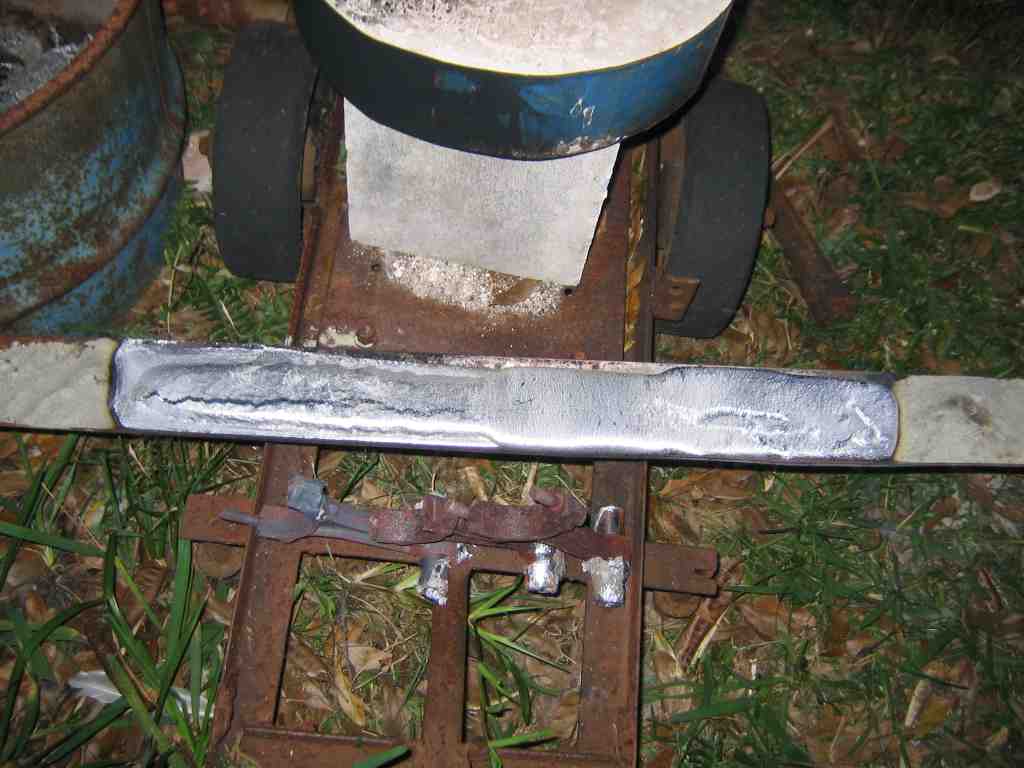
I put the crucible back in the unlit furnace until the ingot
cooled somewhat, and it was still hot enough to add to the ingot.
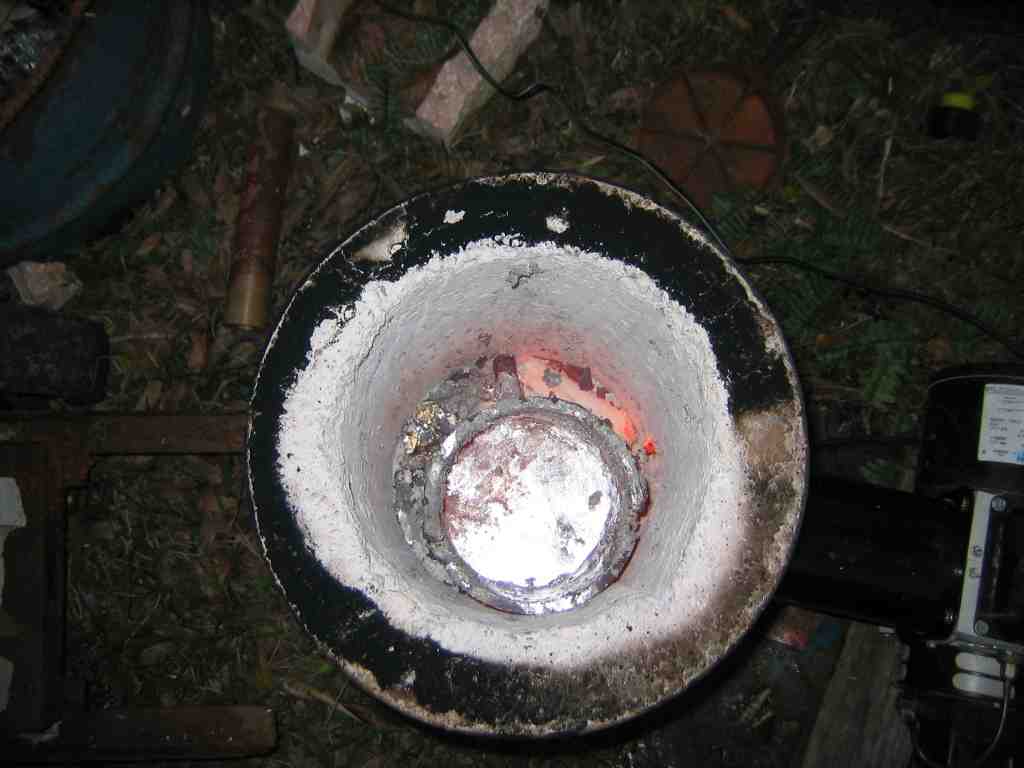
The furnace is still glowing after the double pour.
That's all of the
pictures. I just want to say again how incredibly hot diesel fuel
burns. I am just amazed.
All this is great if you don't mind paying for diesel fuel (or
kerosene, aka HHO [home heatingoil]). If you watch where you buy it,
you can get off road diesel fuel without having to pay the road taxes
on it.
A note about smoke. In the pictures you can see a small amount of
smoke. This was due to the bad alignment and the small burner hole in
the furnace body. At no time was there a cloud of smoke. I feel that
this smoke can be totally eliminated by useing a properly sized furnace
and tuning the burner.
One of the great things about these burners is they just work. You plug
it in (or flip a switch) and it lights and stays lit. Just like in
today's experiment, more time is spent melting metal and way less
futzing around with the burner.
Just as propane is a step above charcoal as a foundry fuel, oil is a
step (or two or three!) above propane, in my opinion.
But diesel fuel is a stop over on the way to waste oil for me and this
Becket oil burner.
Next up is to make a siphon nozzle to use with WMO (waste motor oil).
And then preheaters, and finish the larger furnace, and put it all on a
dedicated cart, and etc. Stay tuned...